IMPORTANT
To avoid all risk of damage to the systems, apply
the safety and cleanliness instructions and operation
recommendations before carrying out any
repair (see 62A, Air conditioning, Air conditioning:
Precautions for repair, page 62A-1) . |
Fault finding for detecting leaks:
Component |
Detection area |
Part to be replaced after
first check |
Part to be replaced after
filling and second check |
Condenser |
Inlet or outlet |
Pipe |
Condenser |
Evaporator |
Connection flange |
Pipe |
Connection flange and/or
evaporator |
Compressor |
Inlet or outlet |
Pipes |
Compressor |
I - ELECTRONIC DETECTORS
Note:
Check for leaks using the electronic detector first
before using the trace detector. |
- This device measures variations in the quantity of
refrigerant in the air and beeps accordingly.
- The device must be initialised before checking.
To do this:
- immobilise the device,
- calibrate the device in the engine compartment,
- do not start the engine.
- This point is then used as standard for detecting the
contamination rate.
This device is highly sensitive: during the detection
process, only follow the line of the circuit as closely
as possible to limit variations caused by other gases.
This device only detects relatively substantial leaks.
Note:
Make sure that the sensor at the end of the rod is
extremely clean and in good condition. |
II - TRACE DETECTORS
WARNING
After injecting dye into the refrigerant, be sure to
indicate this on a label (supplied with the dye
capsule), and the date of the operation.
Position the label so it is visible near to the cold
loop filler valve. |
- Detecting leaks using a tracer involves adding a dye
to the refrigerant, and locating the points of loss
using an ultraviolet light.
Note:
The procedure described must be observed. |
Note:
Use this leak detection method as a last resort
for leaks that cannot be located. |
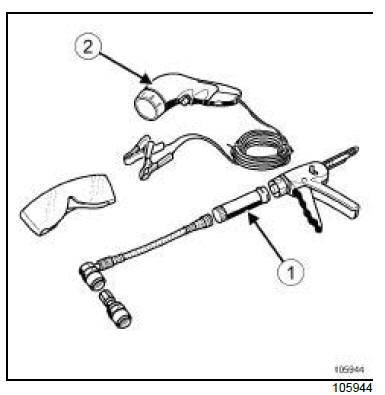
- The procedure for detecting refrigerant leaks uses a
dye which is available as a single-use capsule (1) :
traces of fluid are detected using an ultraviolet lamp
(2) .
- The dye remains in the air conditioning system.
- It is possible to check the status of the cold loop
using the ultraviolet lamp, without injecting the dye
again.
WARNING
To avoid damaging the cold loop components
(corrosions, etc.), do not use dye if the traces
reveal that some product has already been injected. |
- If there is nothing to indicate that dye has been used
previously (label, etc.):
- position a cloth,
- release a small jet of refrigerant through the two
valves,
- light up the valve interior using the ultraviolet lamp,
- check for fluorescent traces.
- Add a dose of detection dye if there are no fluorescent
traces or label.
- Affix a label.
- Record the date when the dye was added.
1 - Injecting dye into the circuit
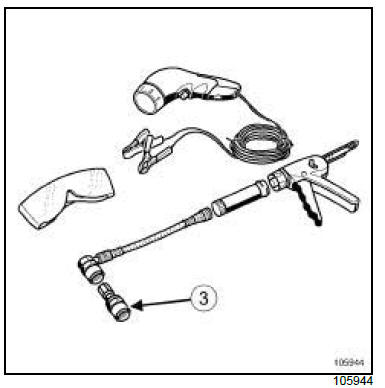
- For vehicles with a single valve, set up the dye injection
system on the low pressure valve by following
the circulation direction of the product and using the
union (3) .
- Inject the dye into the circuit.
- Run the air conditioning system for approximately 15
minutes.
2 - Leak detection procedure
- Carry out an initial check (with the engine stopped)
by sweeping the circuit with an ultraviolet light.
Note:
Use an adjustable mirror wherever access is difficult. |
- If no leak is apparent:
- carefully clean the coolant circuit on the outside,
- run the air conditioning system until the leak is detected
(failing this, check the condition of the evaporator).
WARNING
After injecting dye into the refrigerant, be sure to
indicate this on a label (supplied with the dye
capsule), and the date of the operation.
Position the label so it is visible near to the cold
loop filler valve. |
|